In the second part of this series of articles focusing on identifying and resolving transfer print problems, Sef’s area manager, Holger Beck, addresses transfer parameters for flock and flex this month.
Many users see the transfer parameters specified by the manufacturer as the only option for applying the transfer to the fabric.
However, the manufacturer’s specifications are only recommendations and in all likelihood, everything will be ok when relying on these. But what should be done when plate impressions are caused, the employed fabric is not rated for 165°C, or the process does not work in spite of the specified parameters?
Heat press problems
One problem could be the employed fabric. The transfer press could also present a problem. In all likelihood, defective or poor quality presses are the main cause for adhesion problems. The digital press indicates 165°C and suggests that everything is in order. But whether 165°C is applied is far from certain. Checking the press should therefore be the first priority.
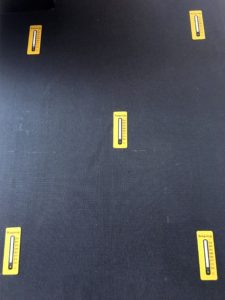
If this reveals significant differences between the indicated and actual temperature, you will need to increase the temperature on the press based on the difference or invest into a new press. The transfer press should be the last place where users cut costs; it is the most important resource for transfer printing.
Protective foil problems
Protective foils could also present a problem. Many users place Teflon foils or paper over the transfer to be pressed in order to either protect the heating plate or the temperature-sensitive fabric. But these protective foils insulate the heating plate; it therefore takes longer for the temperature to reach the required location. If this is further exacerbated by a heavy fabric that needs to be heated up and/or the press does not have sufficient heat output, the hotmelt foil is not heated adequately, cannot melt, and is also unable to adhere to the fabric.
In this case, the protective foil must either be omitted or the temperature needs to be increased. In my opinion, protective foils are not really required in most cases. Neither the polyester frame for the flock or flex foil, nor any previous layers left uncovered in multi-layer applications will contaminate the press. This of course assumes that aqueous PU foils, such as FlexCut Advance or VelCut Evo are used instead of PVC foils.
Temperature-sensitive materials
What can be done to address plate impressions or temperature-sensitive materials? Fabric transfers systems generally always consist of two layers. The applied layer that renders the colour and the hotmelt layer. This hotmelt layer becomes soft during the transfer process, fully conforming to the fabric surface or even penetrating into the fabric, and thus providing the adhesion to the fabric.
The desired wash fastness is assumed as a basis for developing transfer systems. If a wash fastness of 60°C is required, the selected hotmelt must have a melting point that is at least 30°C higher, that is to say at least 90°C in order to achieve the wash fastness. Given that most flock and flex foils appear to have an official melting point of 100°C and 115°C, you might certainly wonder why the recommended temperature is then 165°C? First of all, because at 100-115°C, the foil only begins to get soft but is not yet sufficiently soft to penetrate into the fabric, and secondly, because users do not want to wait until everything under the transfer press has reached a temperature of 115°C. At 165°C on the heating plate, it takes the hotmelt foil 17 seconds to reach the 120-130°C required to become sufficiently soft.
This shows you the available options: you need to achieve 120-130°C at the point of application on the hotmelt foil. Exactly how this is accomplished is irrelevant, at least for the hotmelt. For instance, in order to minimise plate imprints, you can certainly reduce the temperature to 140°C or even 130°C if the time is increased to 30-40 seconds. Conversely, you can also reduce the time by 10 seconds, for instance by selecting 180°C.
Holding up in the wash
How can you now be certain that the combination you determined not only looks good but will also hold up in the wash. A straightforward test for this has never failed me:
- If no adhesion problems appear along the edges while doing so, this will certainly hold up during the wash.
- However, if such adhesion problems show up along the edges, the temperature or time will need to be increased slightly.
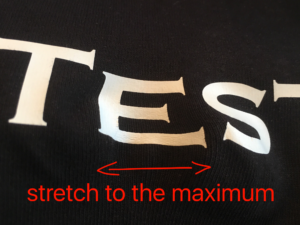
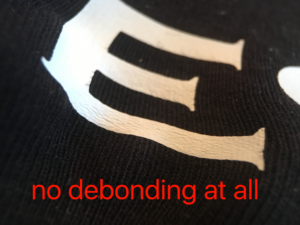

Out-of-the-box thinking is required in particularly difficult situations – for instance on fleece jackets – where even 140°C are insufficient to prevent a plate imprint. While the surface of the fleece jacket cannot be exposed to excessive temperature. This can be achieved by placing the transfer on the fabric and securing it with the adhesive backer or with additional tape strips and then reversing the jacket and ironing from the rear. The plate impression is then on the interior where it does not matter; the outside will at least look dramatically better.
I plan to address the issue of adhesion on problematic fabrics in the next article.
Sef film and vinyl products are available in the UK through Amaya Sales UK.